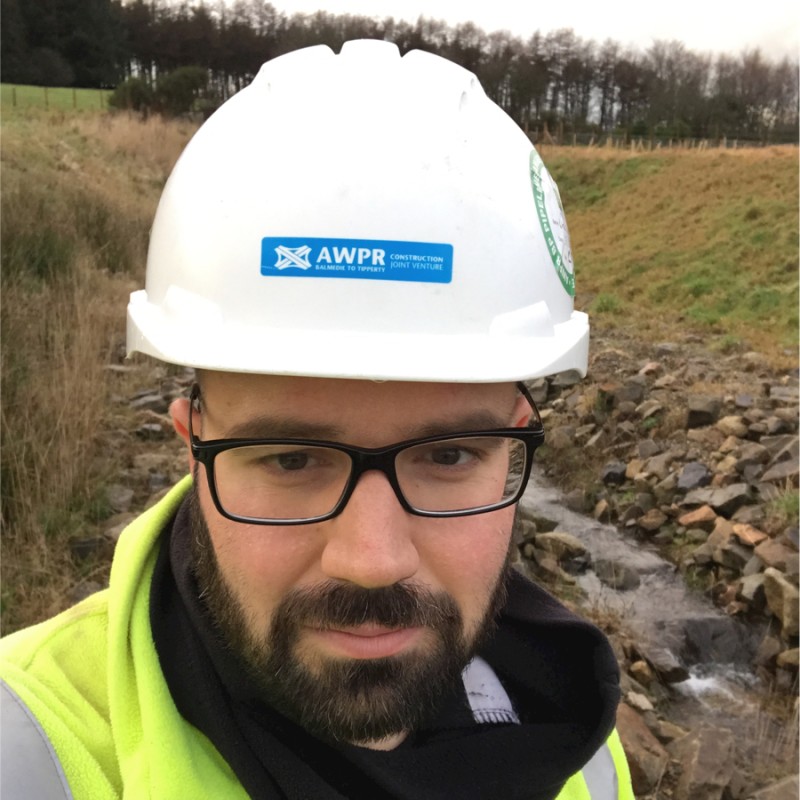
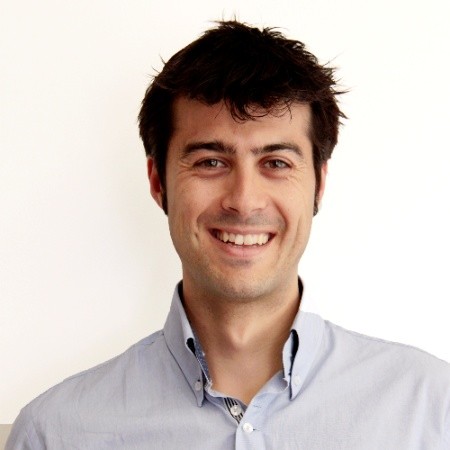
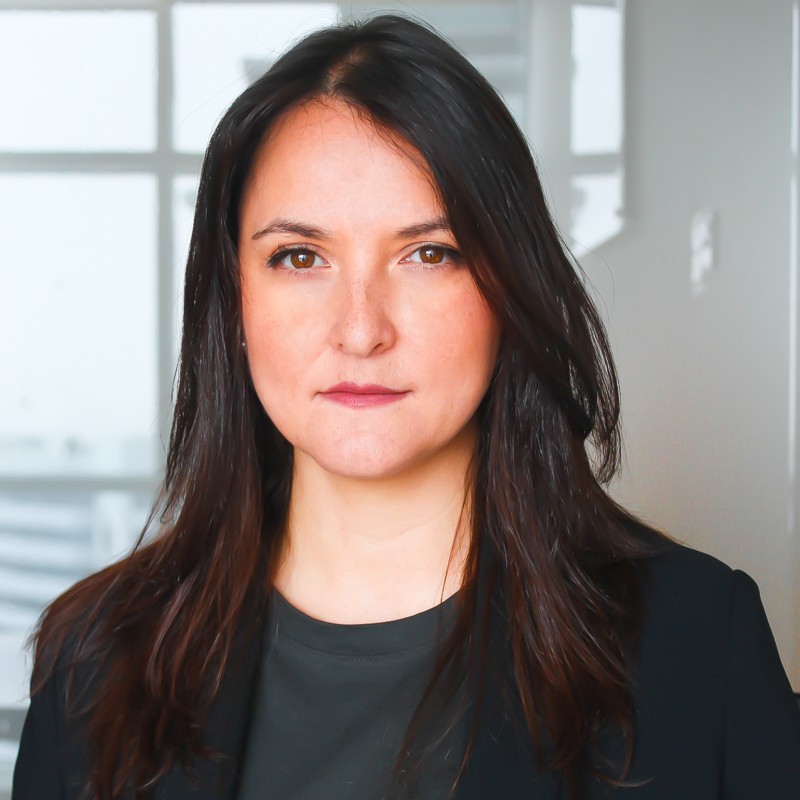
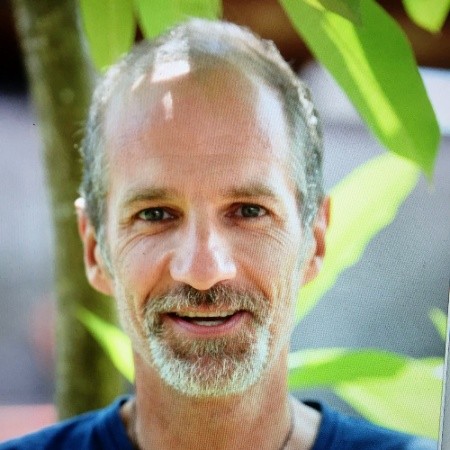
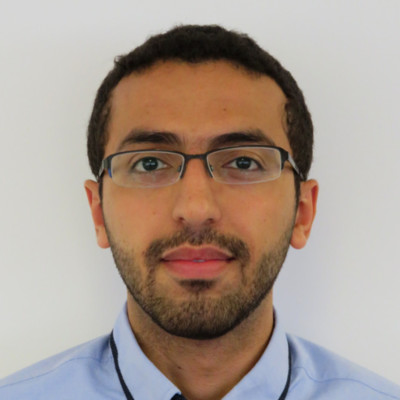
”Once you start using Aphex, it becomes integral to the project. You realise that every team needs a common understanding of their plan”
But delivering the unbelievable infrastructure project that is HS2, are thousands of very real people. People that need to deliver every meter of track, truckload of gravel and cube of concrete that makes up one of Europe’s largest projects, ever.
The delivery of this nationally important scheme is broken into sections, with each section representing a mega-project in its own right. Europe’s largest contractors have been brought in to collaborate, pool resources, and make the 330km high-speed rail line and its stations a reality.
The 80km section of HS2 between the North Chilterns and South Warwickshire is being delivered by the Eiffage, Kier, Ferrovial Construction and BAM Nuttall Joint Venture (EKFB). This vast scope includes 15 viaducts, 6.9kms of cut and cover green tunnels, 22km of road diversions, 81 bridges and 30million cubic metres of excavation.
To understand the realities of managing this behemoth, we spoke to six key individuals about how the scale and complexity of this project exacerbate typical construction challenges. During these conversations, we uncovered new challenges, specific to EKFBs work that many teams wouldn’t have realised at the outset.
EKFB Section Engineer, Mohammed Bolbol had a unique take on the scale and importance of HS2 to the UK, “if you think Facebook, or any social media platform, is meant to connect things and people… Well, at EKFB we are doing that, but quite physically and literally!”. Which did get us thinking about it. HS2 is set to connect 30 million people in the UK; more than the 28.4 million Instagram users that live there.
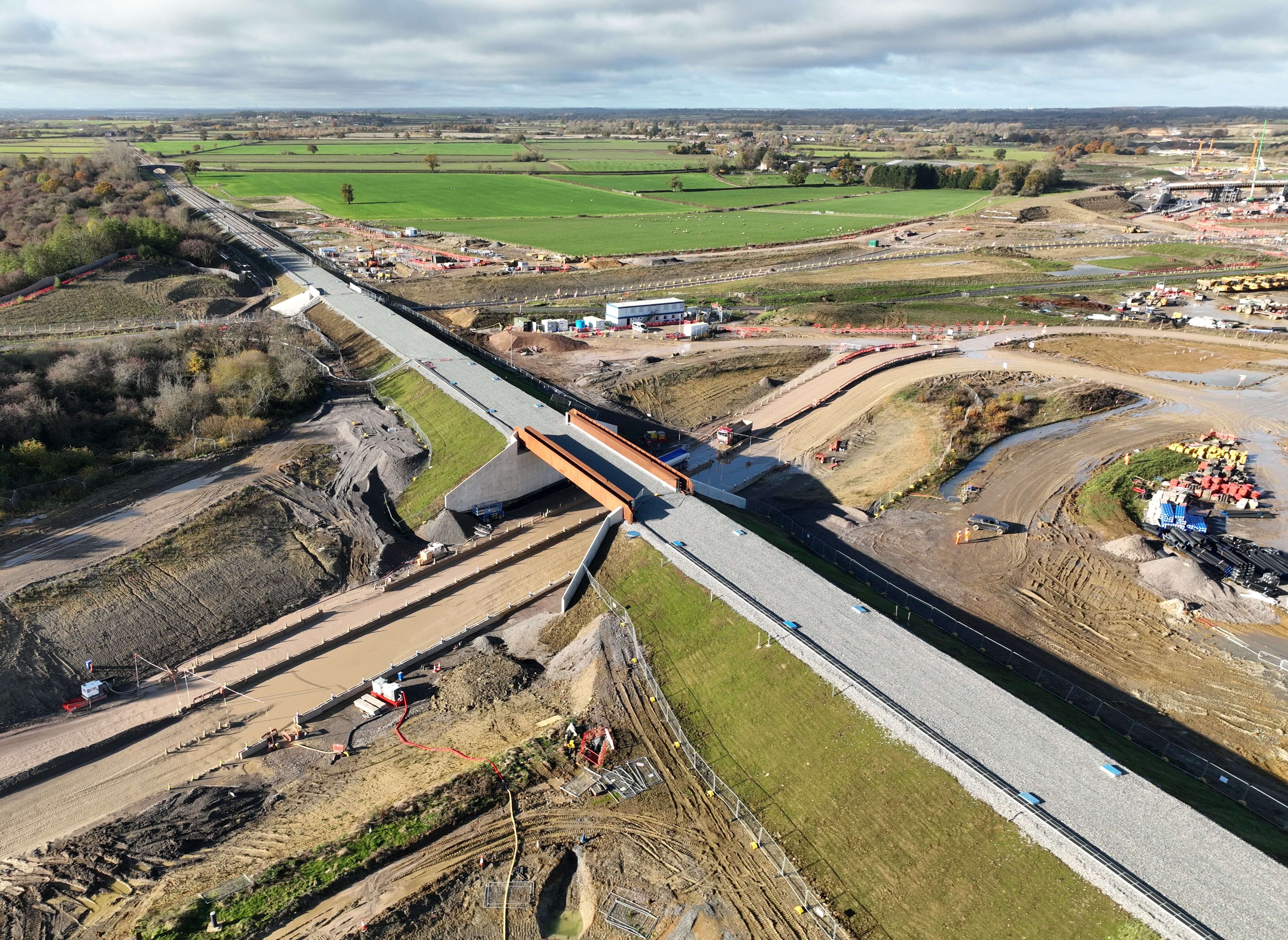
In a somewhat more practical way, Neil Dugmore (EKFB’s NCA Planning Lead), described how the project deals with the extensive geographic area, “We're split into five sections. From the North Chilterns area in south Buckinghamshire to Aylesbury and Calvert, Turweston to Greatworth and Greatworth to Southam. Our works start in Great Missenden in the South and run northwards up to Southam in Warwickshire. Eighty kilometres of civils works, structures, earthworks and utility diversions.
In terms of project management practices, each section operates somewhat differently, with its own teams, milestones, and unique complications. However, speaking to people across these various sections, revealed that the common pain points and difficulties were shared across the board, as were the keys to success.
Sometimes Scale ≠ Complexity
“It is a huge project, but like it's not like I look after an area that's 20 kilometres of entirely new structures.” Alexandros (Sub-Agent) believes that with scale comes a lot of repeatable and familiar components. Mohammed echoes this succinctly, “what is a megaproject? It's a group of smaller ones”.
Similarly, the processes and functions involved in the work itself are not re-inventing the wheel; “Construction is not that difficult.” Says Neil boldly, “Ultimately a bridge is a bridge. Stick together six bridges, and a viaduct, and -large-scale earthworks and it's quite interesting, but it's not massively complicated.”
But sometimes it does…
So, if a megaproject is a sum of its (pretty familiar) parts, why do novel difficulties and unexpected challenges occur? Why do teams have to pivot, respond and resolve situations?
If only we could speak to a team delivering a real-life megaproject to get some answers…
When asked about the day-to-day challenges of their work, it isn’t surprising that many cited all too familiar obstacles that impact almost every construction project. Managing a supply chain, navigating external constraints from site access to working hours, and the dreaded design to construction handover.
Hearing the anecdotes and examples of these issues made one thing very clear. Whilst they might be familiar in origin, the scale and complexity of HS2, with so many moving parts & such large teams, makes this a unique challenge.
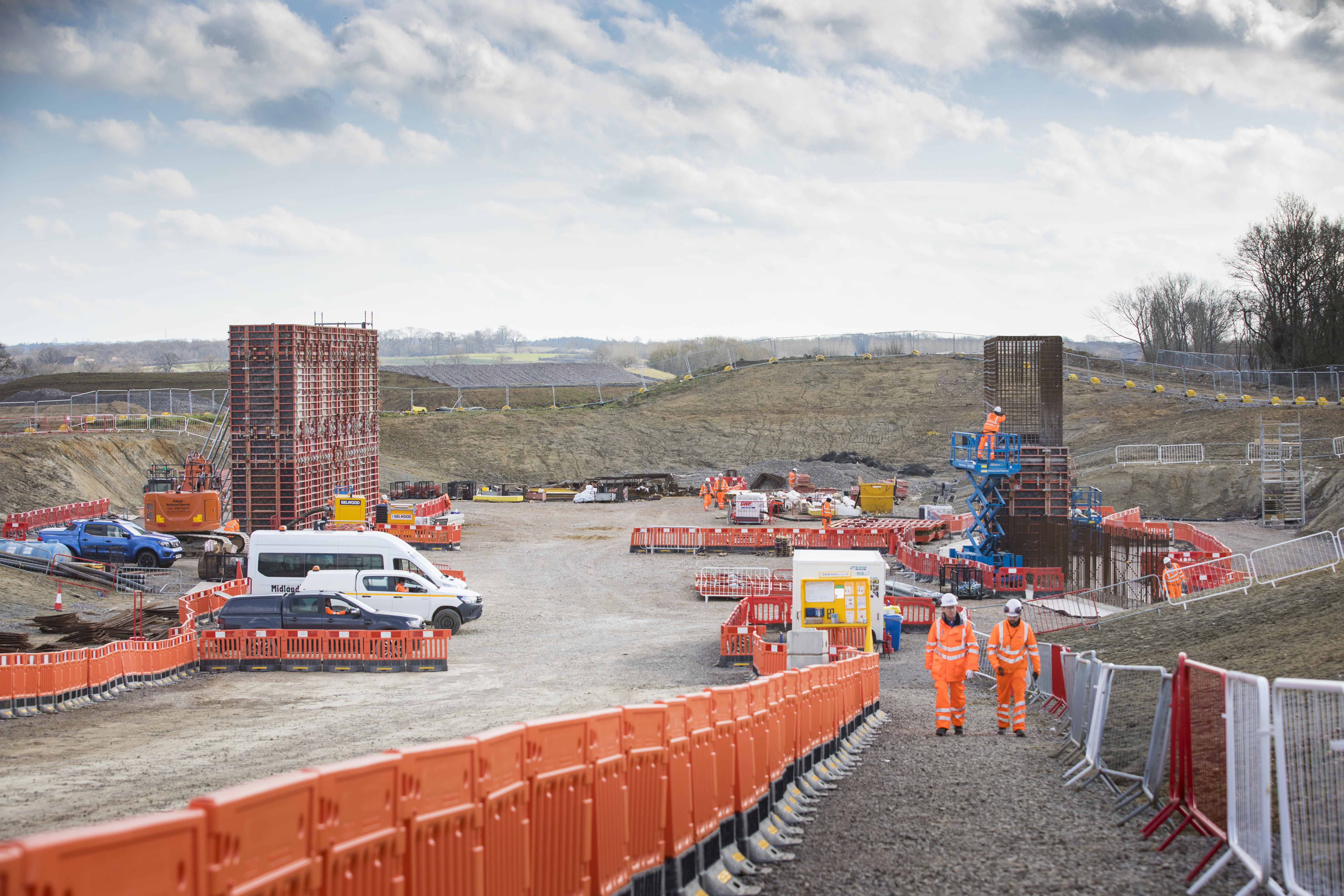
Using digital tools to connect large teams
When you are managing a “typical” project, if such a thing exists, getting plans from a central team to everyone on site is a common challenge. When your project is 800 football pitches in length, simply attending the start of shift briefing stops working. “I would say communication is our biggest issue by far.” Alexandros says, voicing feelings from the entire group,” we’re not even at our peak and have around 100 people involved in delivery, and that’s without counting logistics, planning, and commercial”. In a project with 400 or so engineers and a two-thousand-strong workforce and supply chain spread across 80km the ability to communicate digitally becomes mission-critical.
Today, the EKFB team use a range of tools that help them bridge the physical divide that comes with a massive project. For them, Aphex hosts the actual plan of attack. They utilise multiple projects across the EKFB organisation in Aphex to keep things simple and block out unnecessary complexity that could come with increased project size.
Each project in Aphex covers a unique geographic section of the scheme, allowing the engineers to collaboratively plan their work and know exactly what each other are doing. If someone’s plan changes, everyone can see it and adjust instantly. For Francisco (Senior Planner) and his Aylesbury team, the fact that Aphex is “very easy to use... and keep updated” by his engineers makes it a “powerful communication tool”.
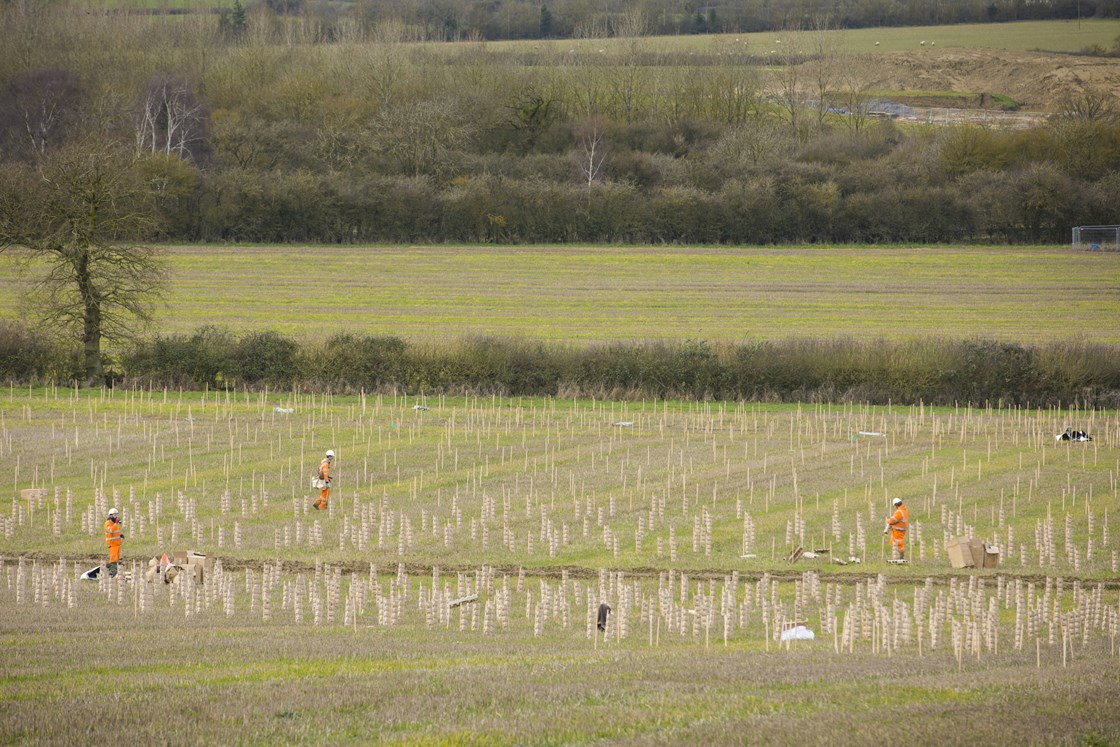
And it isn’t just internal communications that are important. As one of several mega projects active in the UK (Crossrail, Thames Tideway, and other HS2 sections), coordinating with supply chain is just as important. Be it gravel, steel or design drawings, resources are needed on time for the project to succeed. As Neil noted about their design partners, “they’ve got a difficult job. There's a lot of large schemes that are in design at the moment and it is pushing the limits of the resources in the country”.
The project engineers use their Aphex plan in both the weekly meeting with the site supervision team and to lead the daily subcontractor meetings. According to Alexandros, “the visualized sequence of works leaves no room for misunderstanding. It helps smooth out what the team understand they must get done.”
”Once you start using it, it becomes integral to the project. You realise that every team needs a common understanding of their plan."
Mohammed Bolbol
Making progress and issues visible to everyone
Accessing reliable data wasn't easy for the planners across the EKFB project. Its engineers were based in offices across the alignment and spent most of their time out on site dealing with the many logistical challenges that present themselves every day. Leticia (Construction Planner) emphasises this point, “as a planner, you need a lot of information all the time. So, for me, accessing accurate information is core to the role and on a project this size, it’s really one of the struggles.”
To solve this, the EKFB planners rely on Aphex. By establishing a great routine of their engineers updating plans in Aphex on a weekly basis, Leticia says, “the engineers really take ownership of their scope and plans” and Neil adds that, “empowering engineers not only leads to more alignment and quicker communication but importantly for planners, a more accurate bank of data around what’s been happening in the project on the ground”. This accurate view of what is happening on-site and what is causing delay equips everyone in the team with the data they need to both make good decisions, and to communicate these across the entire team.
“Our engineers have the responsibility of managing a piece of work inside Aphex. They implement the program and they keep it updated, we (planners) then create a report which we send across the whole team every week."
Francisco Maestre
Deploying tools that actually save users time
It is the age-old promise of every software – save time, remove admin, remove data entry. Construction teams hear these claims about every piece of software, and every ‘innovation’ they are made to learn and adapt from project to project; but it is rarely true.
Often the QA inspection takes twice as long using the fancy QA software, as it did using the paper form. Or the supposedly ‘simple’ quick-start guide meets a poorly designed system and results in a painful, confusing deployment.
As a leading project in technology adoption in the UK, the EKFB team are somewhat veterans at onboarding new software and understanding its impact, "a step ahead in terms of digital tools” noted Francisco. In deploying Aphex, they took a flexible approach, allowing each of the project sectors to configure it to suit their project management style. By tweaking familiar processes and tech rather than pioneering a shiny new innovative concept, onboarding and adoption were (largely) headache-free and drove immediate benefits across the project.
"Each of our engineers would lose five hours a week if we went back to using spreadsheets to plan. That's 30 hours a week in total for NCA South, so multiplied across the whole EKFB project - could be far more!"
Neil Dugmore
Wrapping Up
For EKFB, finding technology that empowers its teams and helps to refine existing processes was crucial. When teams are up against the clock, have differing approaches, and external pressure; a solution doesn’t solve anything if it adds more work or doesn’t get used.
Aphex has helped in the mega project that is HS2 by helping in the day-to-day, personal experiences that make up the constituent projects. Though the issues that the teams face aren’t too dissimilar to typical infrastructure woes, the context that they exist within is entirely novel.
Our heads are spinning just writing this down, so huge respect to the teams, Aphex users, and interviewees involved for all their hard work in delivering this massively impressive project!
Heading
Lorem ipsum dolor sit amet, consectetur adipiscing elit. Suspendisse varius Duis cursus,