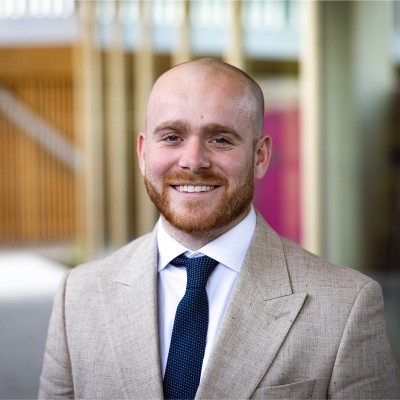
Aphex becomes the source of the information for the trades to know where they are working, at what time, and in what sequence.
The project: An amenities hub
In 2024, Mace successfully delivered ‘The Hub’ in Cambridge for a global pharmaceutical company on schedule.
Targeting a BREEAM outstanding rating with innovation in both materials and methods used, the project was a tremendous success.
'The Hub' will support the 17,500-strong workforce operating on one of the UK's biggest biochemical campuses for years to come.
But like every major project, there were challenges along the way.
We discussed the project with Oliver Borley, Planning Manager at Mace, to learn more about how the team was able to stay on the same page through a complex build.
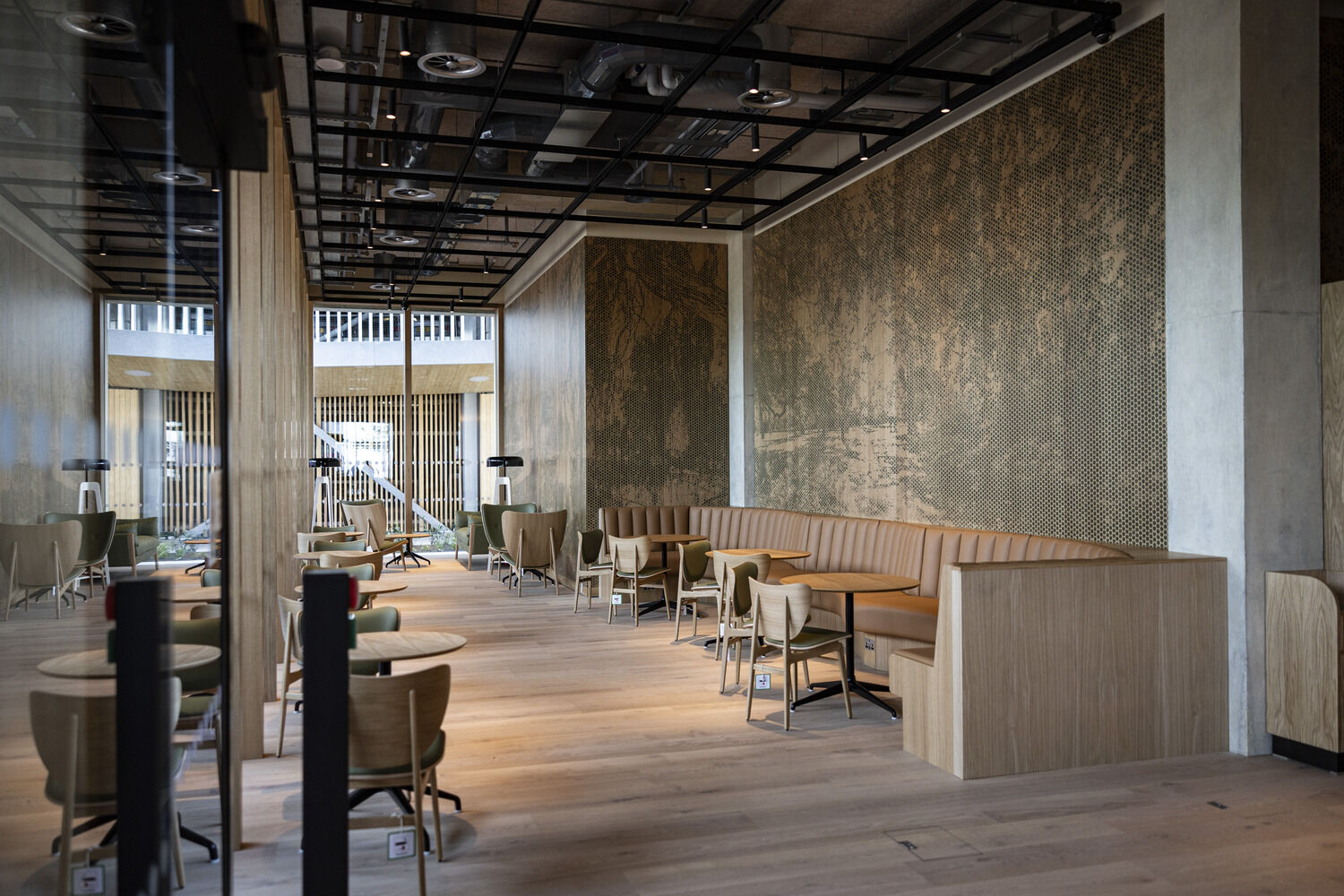
The root of the problem
As the Mace team explains, coordination between trades is critical to the timely completion of any project.
With multiple stakeholders helping to deliver a complex sequence of works, buy-in and accountability from everyone is key to staying on target.
In past projects, these stakeholders were often coordinated using a multitude of disconnected spreadsheets and documents. The problem with this approach is that critical information is often siloed rather than shared, and issues can remain unresolved until they arise on-site.
The Mace team's plan? Bring on Aphex to make sure everyone on the project knows exactly what’s going on — in real-time.
“Aphex becomes the source of the information for the trades to know where they are working, at what time, and in what sequence.”
Oliver Borley, Planning Manager
Starting with the subcontractors
The project team identified that if they could initially coordinate with the subcontractors producing the biggest pieces of work, they could quickly achieve collaboration and accountability for a large part of the scheme.
Keeping it relatively simple at first, the supply chain began building their plans in Aphex, using the Maps feature to mark off where activities were supposed to happen.
This allowed the team to not only talk through the plan for the week, but also visually communicate where tasks, teams and resources needed to be, thereby avoiding any potential clashes on-site.
This quickly resolved some of the miscommunication they had seen earlier in the build.
Expanding to the whole project
Seeing these wins, Oliver and the team decided that it was time to roll out the Aphex for the whole project.
The first step was to assist every team in creating their look-ahead plans in Aphex, which created a point of truth for the project as a whole.
These plans were completed prior to the team’s planning meetings. In the meeting, the team used Aphex’s Gantt and Map views to talk through their plans for the week ahead. This allowed everyone to get on the same page much more quickly — and even made it easier to spot and solve issues in the room.
Subcontractors were able to quickly filter the plan to their own work and talk it through with the delivery team, with their updates ultimately improving the fidelity of the project plan as a whole.
The result? Stronger relationships between the trades, better coordination, and reduced admin for the planning team, who no longer had to spend hours combining multiple Excel spreadsheets and creating sequence decks within PowerPoint.
All of these were generated within Aphex, resulting in considerable time savings.
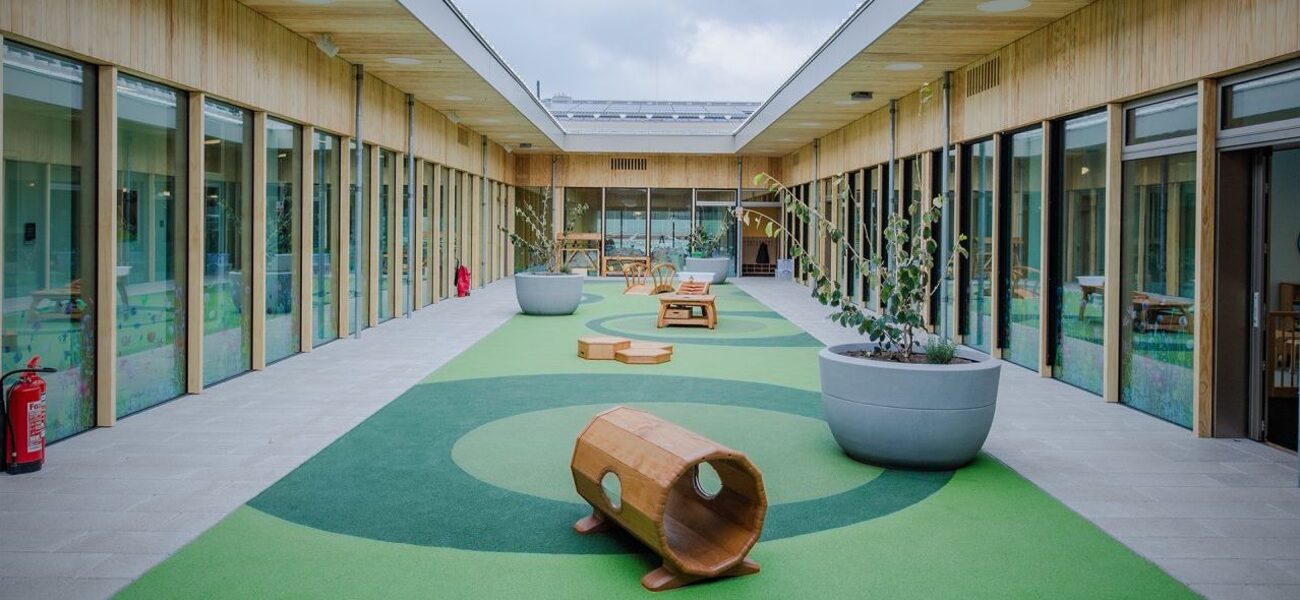
“The new milestones feature has massively helped”
As the project was drawing to an end, the team needed to understand any delays to key milestones, in order for resources to be reallocated to ensure critical deadlines were met.
Enter Aphex Milestones, which allows teams to create a milestone task with a hard due date. This allows the team to monitor progress, measure reasons for delays, and see how the team is performing compared to the contractual programme.
Using this feature, Oliver and the planning team were able to track delays, communicate these to the team, and empower everyone to contribute to a solution.
“The new milestones feature has massively helped with void closures and helped us track planned vs actuals.”
Oliver Borley, Planning Manager
Stronger communication, more accountability, and better results
By the end, the project team — including subcontractors — were actively collaborating, allowing them to solve issues early before they had a chance to become a headache on-site.
This ultimately led to the supply chain becoming more accountable and certainly empowered by the ownership of their plan.
The proof is in the pudding: With Aphex, the Mace team reduced the number of disputes and delays. And even better, they created a better working environment for everyone on the project.
Finally, we asked Oliver if Aphex would play a role in delivering the next phase of the project in Q1 2025. His reply: “100%. Aphex has quickly become part of our team’s ‘toolbox’, and will help us with future projects."
Heading
Lorem ipsum dolor sit amet, consectetur adipiscing elit. Suspendisse varius Duis cursus,