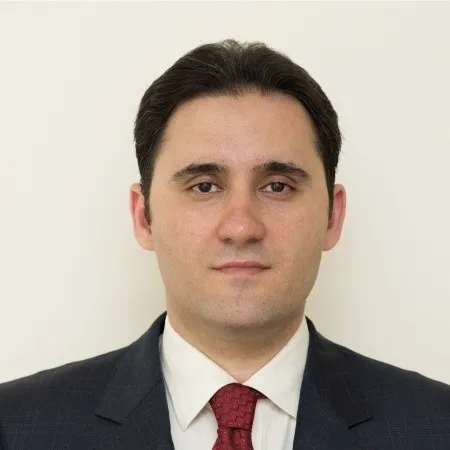
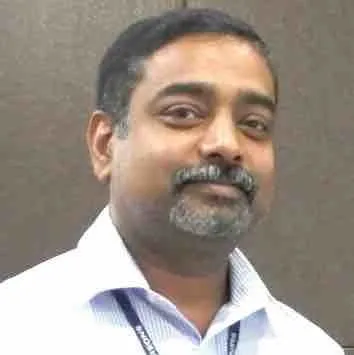
With Aphex, our whole project team works in a single connected plan. Across disciplines and areas, roles and levels of detail.
When finished, the project will transform traffic flow in and around the Airport precinct by diverting around 10,000 trucks daily from local streets, reducing travel times and congestion.
The design and construction of this landmark project is being delivered in joint venture by John Holland and Seymour Whyte (subsidiary of VINCI Construction) JHSWJV.
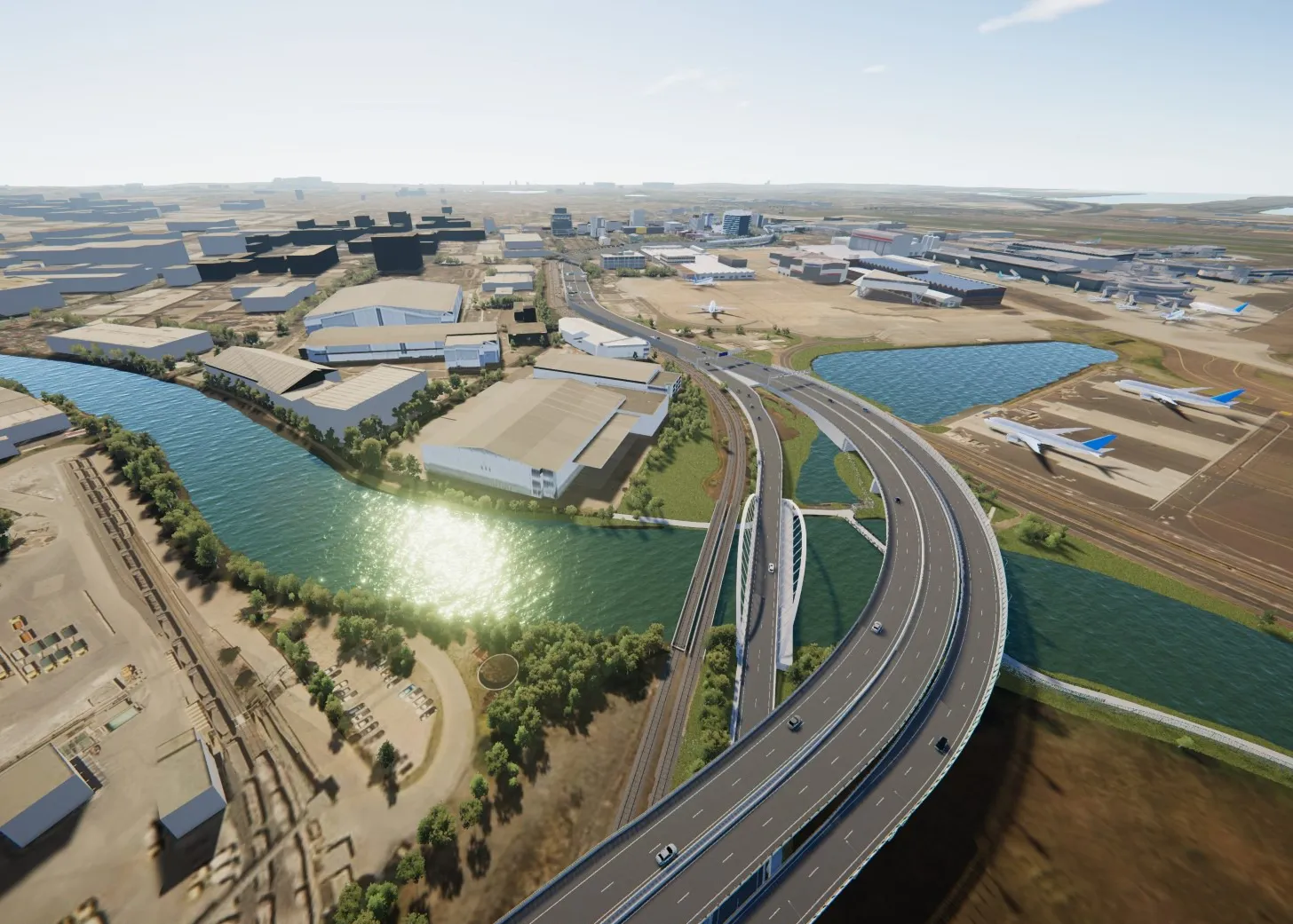
The project is enormous - involving 19 new bridges, 8,500 tons of steel structures, 6.5km of piles, and 340,000 cubic meters of earthworks. But what is unique about the Sydney Gateway project is the extreme constraints the delivery team must navigate. The project interfaces some of Sydney’s busiest roads and is within the highly regulated airport precinct. In many areas, the works are sandwiched between a rail line and the airport boundary and above major city utilities. Everything we do needs to be meticulously planned. “Missing an interface can cause months of delay with our strict stakeholder approvals,” said Bruce Latifi, Planning and Controls Manager for the project. “Everything we do requires a combination of local, state, and federal government approvals and needs to comply with aviation, rail corridor, and major utility requirements.”
From the start of the project, the leaders from John Holland and Seymour Whyte knew that some of the processes and tools they had used on previous projects would be pushed beyond their limits on Sydney Gateway and the team worked hard to define methods that would set them up to succeed. “Before we got on-site, our team looked at the best examples of how previous projects managed to coordinate and communicate their plans,” explained Bruce, “everything came back to versions of 4-week-lookahead spreadsheets.”
The Gateway team knew that to deliver their project to a world-class standard, their team needed to spend less time formatting and emailing spreadsheets. After experimenting with Aphex, the project decided it needed a single platform to manage its lookahead plans. Within a few weeks, the project team had been set up, trained, and free from heavily formatted spreadsheets.
“Before we got on-site, our team looked at the best examples of how previous projects managed to coordinate and communicate their plans, everything came back to versions of 4-week-lookahead spreadsheets.” Bruce Latifi, Planning and Controls Manager
Driving a “one team - one plan” approach.
When a project team has over 150 engineers across major earthworks, structures, utilities, and traffic disciplines, it can quickly become fragmented, with sections focusing on their siloed scope. For the John Holland Seymour Whyte Joint Venture team, driving a “one team” culture across disciplines, joint venture partners, and supply chain was crucial to coordinating such a complex project.
To connect the team to a single plan, the project decided to take the top-down approach within Aphex, importing a high-level skeleton of interlinked work ready to be broken down and detailed by all engineers in a single plan. “Every month I import six weeks from our level-4 program to the engineers, giving them key dates and a structure of a plan to break down to level-5 detail connected to our Master Delivery Plan.” Vivek Manickam, Planner, Sydney Gateway
This approach delivers a single connected lookahead plan across the entire project and aligns it with project-wide goals in Primavera P6 - a literal “one plan” approach. “The team is all working in a single connected plan,” explained Vivek, “different areas can work together detailing their sections before coming together as an entire project.”
To control and standardise the cadence of planning across the entire project, the team not only works on a single plan but also follows a single planning routine. Every team across the project has a mid-week deadline to update their plans in advance of a Thursday Planning Meeting. After plans are presented and reviewed as a team, the entire project’s short-term plan is locked down every Friday. Every Monday, performance against the previous week’s plan is reported and reviewed with each team across the project.
Since deploying Aphex, the project has had consistent weekly reporting of the progress of work and a better understanding of delay drivers. Every Monday, reports are generated from the Aphex Insight App and shared with management for weekly performance reviews. “We have a lean planning and controls team for a large project. Moving our lookahead plans out of spreadsheets means we have weekly automated and consistent reports for project managers.” Bruce Latifi, Planning and Control Manager.
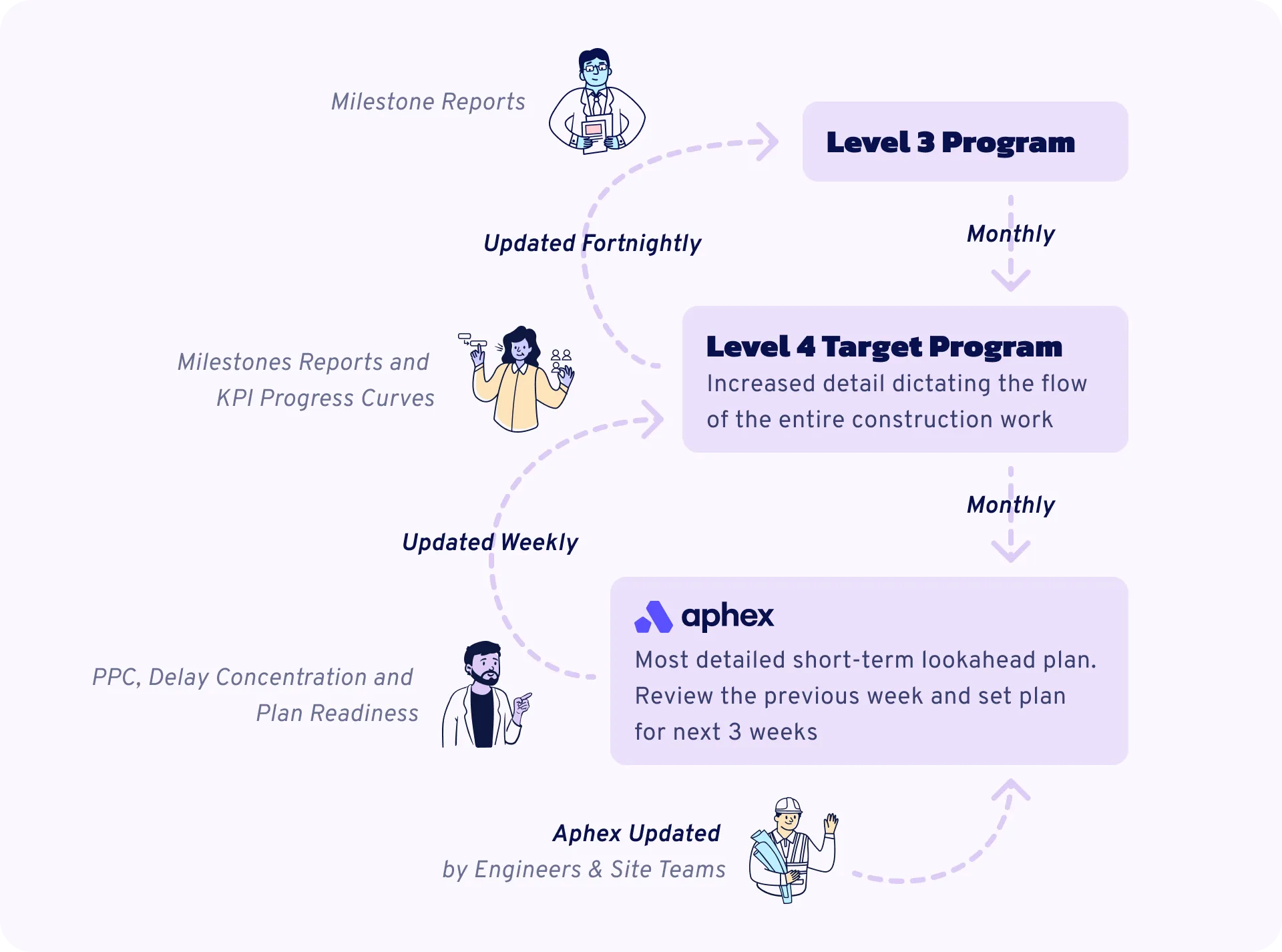
“We have a lean planning and controls team for a large project. Moving our lookahead plans out of spreadsheets means we have weekly automated and consistent reports for project managers.”
Bruce Latifi, Planning and Controls Manager.
Clear Coordination of Site Teams
At a site level, teams face significant coordination challenges due to the volume and scope of work across the major disciplines and interdependencies and interfaces between various disciplines, management of traffic control, and relocation of major utilities.
Every week, the project’s Engineering teams come together in the on-site planning room to present their plans; how their teams are progressing against the current week’s plan, followed by reviewing planned work in the upcoming 4-week lookahead. During the meeting, the plan is presented and updated in real-time. “Weekly review sessions are a great place to discuss site coordination and flagging interface issues,” noted Bruce Latifi, “our Site Supervisors and Traffic team use the map view to understand site logistics and traffic control.”
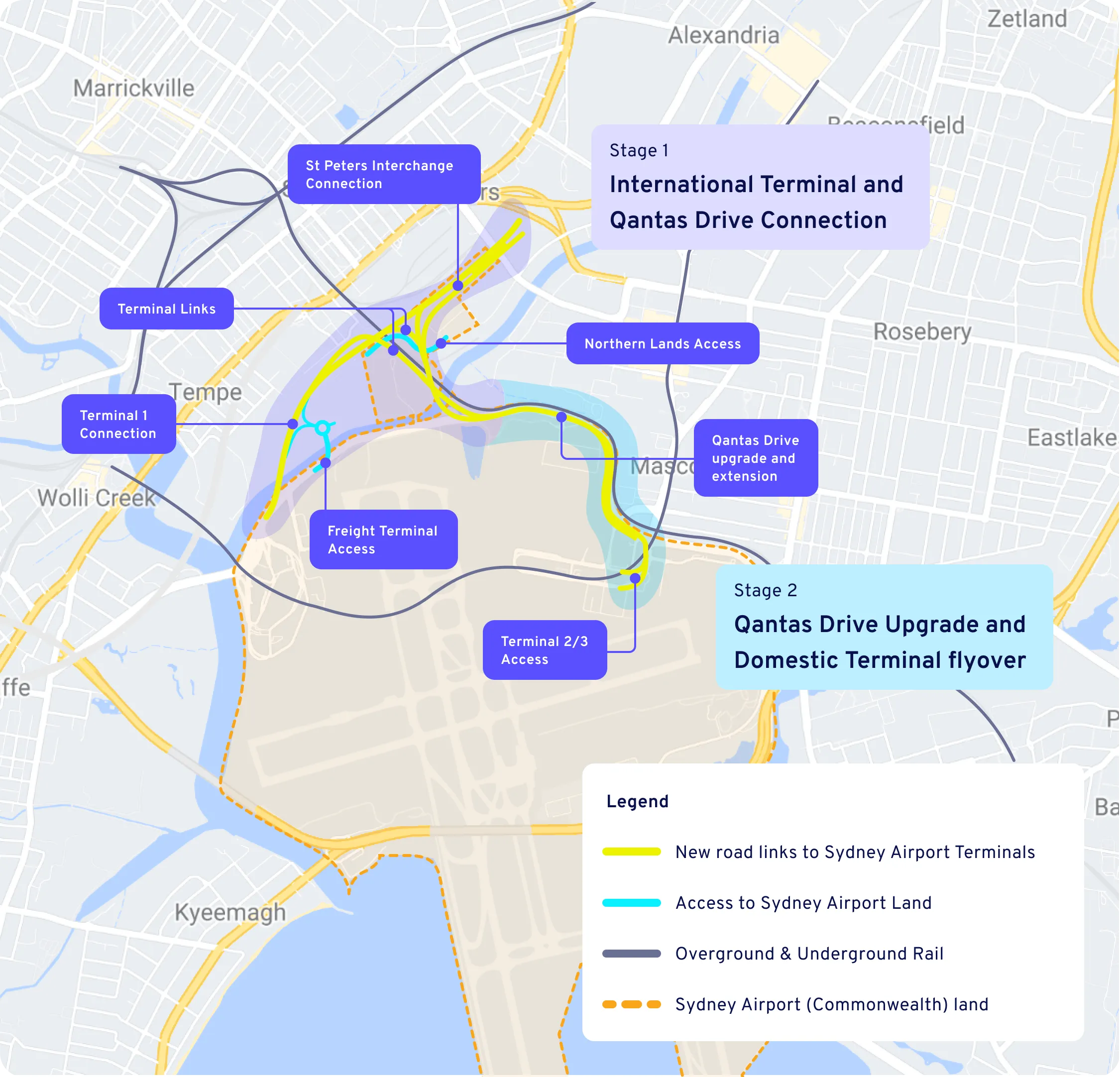
While it is true that no software or tool delivers a construction project, for a strong project team like that from John Holland Seymour Whyte Joint Venture on Sydney Gateway, empowering their teams to plan and coordinate work in Aphex collaboratively allowed everyone to spend more of their time delivering the project.
Heading
Lorem ipsum dolor sit amet, consectetur adipiscing elit. Suspendisse varius Duis cursus,